CREACIÓN DE LOS PRODUCTOS:
Su fabricación es un proceso que consta de los siguientes pasos:
Partiendo de un bloque de madera, habitualmente de cedro, se divide en tablitas a las que se le hacen unas hendiduras para colocar las minas.

A continuación se aplica pegamento en los surcos de las tablillas, se colocan las minas de grafito en una de ellas y se coloca la otra encima.

Una vez seco el pegamento, otra máquina se encarga de practicar hendiduras a ambos lados de la tabla por donde se separarán los lápices.

Primero, se cortan desde la parte superior hasta la mitad. Y después desde la parte inferior hasta encontrar el corte anterior en la mitad de la tablilla. Así, de las tablillas encoladas obtendremos nueve barras similares a lápices.

Por lo tanto, recuerda que las minas no son metidas a presión dentro del lápiz, sino que se colocan entre dos tablillas ranuradas de madera.

Producto final
El lápiz es uno de los objetos más comunes de la escuela, y útiles más usados para escritura borrable, es el lápiz.
CREACIÓN DE LAS BOMBAS DE AGUAS EÓLICAS:
Paso 1: Prepara las ruedas y el engranaje.
Buena parte de los materiales para esta bomba de agua eólica son piezas aprovechadas de bicicletas, que han sido adaptadas para que funcionen para este fin. Ese es el caso de los engranajes, para los que tendrás que emplear la pieza que ves en la imagen (el cassette) y, como ves, colocar pernos en su perímetro.
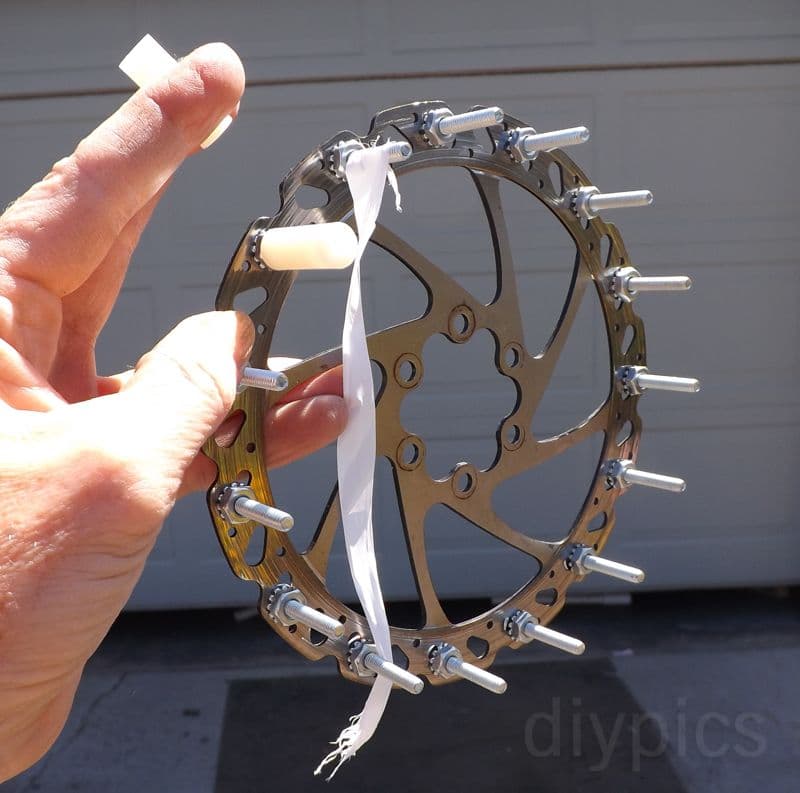
Para la pieza que irá en la parte superior de la bomba, usa pernos que sean cortos; mientras que para la que van en vertical, los largos serán más adecuados.
Acto seguido, une el engranaje horizontal al eje de una rueda de bicicleta. Por otro lado, une a la pieza la llanta de otra rueda con tres soportes metálicos.
Ahora, necesitarás un trípode que sea robusto para, en su parte superior, fijar una pieza en T para la conexión de tuberías PVC. En esta pieza tendrás que instalar la estructura de ruedas que has creado. En este caso, se ha optado por hacerlo con un par de piezas de madera circulares. Posteriormente deberás instalar la pieza vertical en la horizontal de la pieza conectora para PVC, de forma que no impida la rotación de la misma.

Paso 2: Crea las velas de viento.
Aunque inicialmente para este proyecto se optó por piezas de tela recubiertas de láminas de plástico, lo cierto es que tras realizar varias pruebas se comprobó que el sistema no era suficientemente eficaz. Por ello, prepara cinco velas de viento con PVC o con estaño y fíjalas directamente a las llantas de la bicicleta.
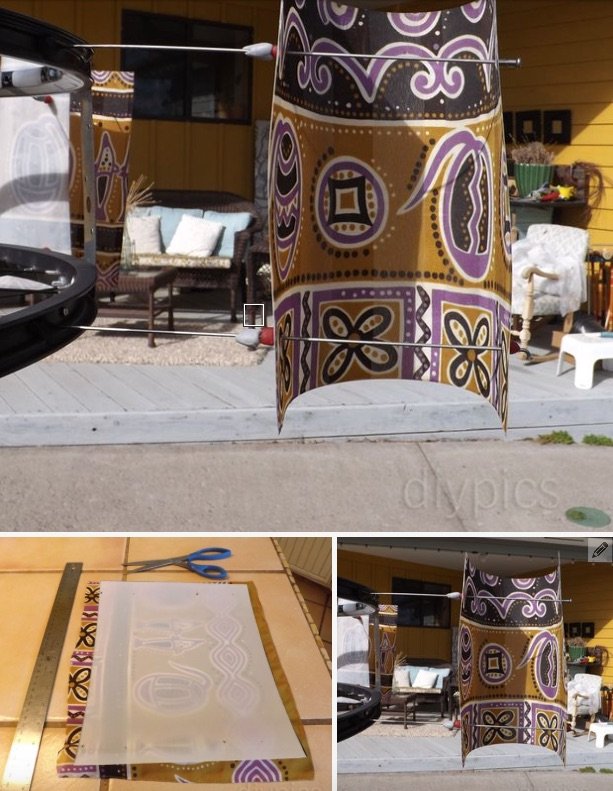
Paso 3: Instala las velas.
En este paso tendrás que perforar cinco agujeros de tamaño suficiente para que por ellos pase un radio de bicicleta. De hecho, vas a tener que insertarlos a la llanta de manera que queden bien sujetos, por ejemplo mediante epóxido, muy utilizado en fontanería por su eficacia para la adherencia.
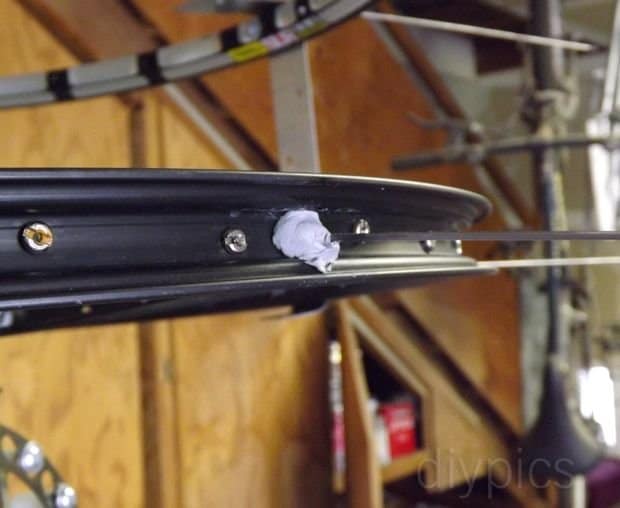
Una vez se seque el epóxido, las velas también tendrán que fijarse a los radios de la bicicleta. Asegúralas de nuevo con el mismo material y, si quieres reforzarla la estructura todavía más, atornilla los radios para evitar que las velas se caigan.
Paso 4: Fabrica el conector de la bomba.
Si revisas el mecanismo vertical, verás que en la parte trasera de los pernos que habías colocado en los cassettes hay una pequeña bola roja. En realidad, son dos, esta y otra fijada al pistón de la bomba de agua, gracias a las que el generador eólico y la bomba se conectan de manera que la fuerza del viento se transfiere a la bomba de agua.
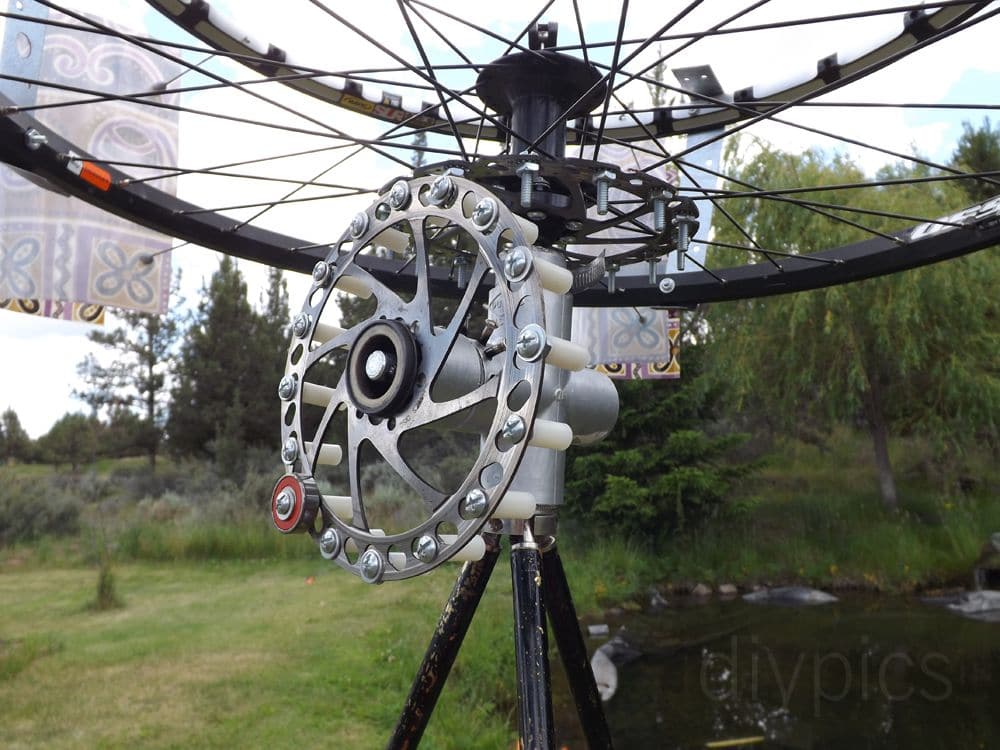
Este conector está fabricado sencillamente con una tubería de PVC. En él se han insertado además varios radios de bicicleta, simplemente calentando el plástico, por ejemplo sobre el fuego de una cocina. Asegúrate de que esta parte del sistema sea lo más ligera posible ya que, de lo contrario, necesitará más aire para funcionar.
Paso 5: Crea la bomba de agua.

Para crear la bomba de agua necesitarás básicamente tubería de PVC y un conector en T. Si sigues el modelo de la imagen no debes de tener ningún problema para que todo cuadre. Paso 6: Fija la turbina eólica y la bomba de agua.
Para que el sistema se mantenga erguido fija una vara metálica en el suelo, de manera firme, en el lugar en el que quieras ubicar el equipo. Une la vara metálica con la parte exterior de la bomba mediante pinzas de tornillo.
Acto seguido, coloca la turbina de viento sobre la bomba de manera que esté lo suficientemente alta como para que el brazo conector quede bien extendido. Finalmente, asegúrate de unir el conector con la rueda en horizontal y con el pistón de la bomba.
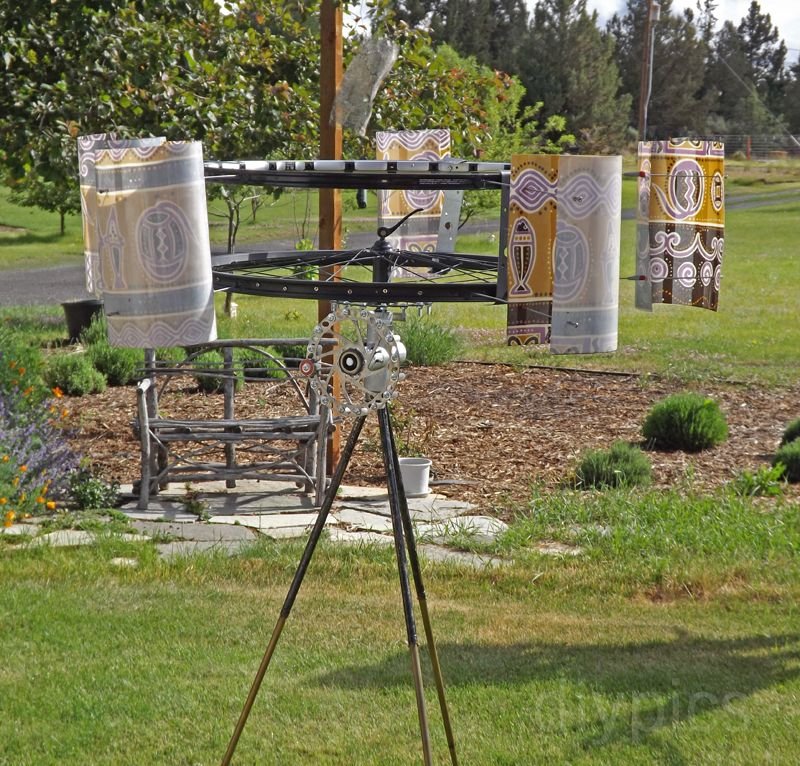
Como el sistema puede resultar algo frágil, lo ideal es que lo refuerces mediante su instalación sobre un poste de 4×4, lo que eliminará movimientos no deseados.
Con todos estos pasos, la bomba de agua eólica estará lista. Sin embargo, observando su funcionamiento y tras recibir muchas sugerencias, el impulsor de esta idea ha aplicado algunas mejoras para aumentar el rendimiento. Son las siguientes:
- Sustituir el trípode por una tubería metálica a lo largo de todo el sistema.
- Aproximar al suelo la válvula de manera que no sea necesario bombear el agua a tanta altura.
- Sustituir el pistón y el brazo de PVC por amortiguadores de bicicletas.
- Desenganchar las velas por su parte inferior y dejarlas ancladas a la estructura por la superior, de manera que queden en ‘modo ataque’, lo que aportará más flexibilidad y favorecerá el empuje.
Ahora sí, con estas últimas recomendaciones ya está todo listo para que puedas poner en marcha tu bomba de aire propulsada por el viento.
CREACIÓN DE EL PAPEL:
Se talan árboles con diferentes tipos de fibras, tanto resinosas como frondosas. Los árboles seleccionados deben poseer un diámetro aproximado entre 15 - 30 cm. Se desmochan (eliminación de la copa) y se quitan las hojas y las ramas, dejando el tronco limpio. Después los troncos se transportan a la fábrica para someterlos al proceso de preparación de la pasta.
2. Para preparar la pasta se cortan los troncos en rollizos de 2 - 2,5 m. Una vez hecho esto se introducen en una máquina cilíndrica con cuchillas en su interior que se encarga de descortezarlos, dejándolos limpios y preparados para el proceso de astillado (a excepción de la preparación de la pasta mecánica clásica que no precisa astillado).
3. Tras el astillado de la madera se procede a la realización de la pasta según la que se desee obtener ya sea mecánica, termomecánica, química ó quimicotermomecánica. Posteriormente se lleva a cabo el blanqueo para eliminar la lignina y otras materias que no son fibras. Aunque el gas de cloro y el dióxido de cloro son extremadamente eficaces en el blanqueo de fibras de madera, las consideraciones ambientales han llevado a la eliminación gradual de dichas sustancias químicas en este proceso. Como otras opciones están el blanqueo con ozono, con enzimas o con peróxidos, que eliminan la contaminación.
4. A continuación se lleva a cabo la depuración, que, dependiendo del tipo de fibra necesitará unos u otros tratamientos.
En el caso de las fibras primarias necesitará pasar por el púlper para individualizar las fibras agitando las hojas de pasta con una hélice.
Después necesitará una pasada por los despastilladores que hacen la misma función que el púlper pero de manera más enérgica para que no queden partículas mal desfibradas.
El refino sería la última parada antes de la fabricación del papel propiamente dicha. Este tratamiento dota a las fibras de celulosa de las características necesarias para producir el papel. Se llevan a cabo en pilas holandesas, refinos de discos o cónicos.
En el caso de las fibras secundarias (papelote), se las introduce dentro del púlper para deshacer el papelote y eliminar impurezas.
Tras ello, se procede al destintado usando detergentes, dispersantes y espumantes a través de 4 técnicas distintas. Dichas técnicas son el lavado, el destintado por flotación, por enzimas o combinando estos procesos.
5. En la tina de mezclas se realiza la formulación del papel, añadiendo fibras, cargas y aditivos que se precisen. Esta mezcla pasa a una tina de reserva y a veces se da un nuevo refinado.
Tras la tina de mezclas se lleva a cabo la depuración de la pasta que eliminan las partículas indeseables.
Tras la tina de mezclas se lleva a cabo la depuración de la pasta que eliminan las partículas indeseables.
6. La caja de entrada regula la pasta de acuerdo con parámetros como la densidad, la consistencia y el caudal, homogeneizándola para luego, pasar a la mesa plana a través del labio que posee la caja de entrada.
La mesa plana es una tela sin fin (metálica o plástica) donde se formará la hoja de papel. En esta etapa se decidirá la orientación de las fibras. Si el chorro de pasta va más rápido que la tela las fibras tienden a orientarse en todas las direcciones. Si por el contrario va más lento, las fibras se orientarán en el sentido de avance de máquina.
La mesa plana es una tela sin fin (metálica o plástica) donde se formará la hoja de papel. En esta etapa se decidirá la orientación de las fibras. Si el chorro de pasta va más rápido que la tela las fibras tienden a orientarse en todas las direcciones. Si por el contrario va más lento, las fibras se orientarán en el sentido de avance de máquina.
7. Una vez la pasta esta distribuida sobre la mesa plana comienza el proceso de desgote. Se utilizan distintos mecanismos de desgote empezando por los rodillos desgotadores que soportan la tela y ayudan a eliminar el agua.
Otro elemento de desgote en las primeras zonas son los foils, que están compuestos de barras que no giran, la tela se desliza sobre ellos y producen un efecto de aspiración progresiva.
Tras los mecanismos anteriores encontraríamos las cajas aspirantes ó de vacío que realizan el desgote más enérgicamente mediante una aspiración progresiva con bombas de vacío.
El cilindro aspirante es el último elemento de desgote y consta de una camisa metálica perforada que gira a la velocidad de la tela.
Al final de la mesa plana está el rodillo mataespumas ó Dandy Roll que dota de mayor consistencia, mejor formación, lisura y uniformidad a la hoja. Por supuesto, contribuye al desgote y en algunas máquinas se utiliza para verjurar y hacer marcas de agua.
8. Inmediatamente después de la tela el papel pasa por las prensas, donde se consolida la hoja forzándola a un contacto con el rodillo. La humedad se queda en los fieltros y el papel pasará posteriormente por la sequería.
La sequería es un conjunto de secciones de rodillos que aplican calor y van a distintas velocidades. Esto crea problemas de estabilidad dimensional por lo que necesitará un tratamiento superficial, que supondría la siguiente fase.
La sequería es un conjunto de secciones de rodillos que aplican calor y van a distintas velocidades. Esto crea problemas de estabilidad dimensional por lo que necesitará un tratamiento superficial, que supondría la siguiente fase.
Dentro de los tratamientos superficiales tendríamos 3 máquinas distintas; la Size-Press, Gate-Roll ó la Bill-Blade. La primera es la más utilizada y se usa para colocar una capa de ligante para evitar problemas de arrancado y si hiciese falta otra capa de estucado. Todo ello se aplica a través de prensas blandas que presionan el papel.
Las lisas son el último paso de fabricación. Son grupos de rodillos metálicos superpuestos que se encargan de dar lisura y regular el espesor de toda la hoja.
Finalmente el papel es enrollado en el Pope para mandarlo a la fase de acabados.
9. Una vez hecho el papel, se puede aplicar una salsa de estuco que ennoblecerá su acabado y lo dotará de mejores condiciones de imprimibilidad. El estucado esta compuesto por pigmentos, ligantes y aditivos.
Este acabado se podría aplicar mediante dos métodos distintos:
Este acabado se podría aplicar mediante dos métodos distintos:
- Estucadora de rasqueta. Es el más común. Se aplica el fluido mediante un rodillo y después se iguala y dosifica mediante una lámina de acero que puede ser rígida o flexible, para aplicar más o menos cantidad de capa.
- De labio soplador. Un rodillo aplica un exceso de fluido que luego es eliminado por un flujo laminar de aire a presión, lo cual nos permite depositar altas cantidades de capa de estuco. Se emplea en papeles arte y altos brillos.
- De labio soplador. Un rodillo aplica un exceso de fluido que luego es eliminado por un flujo laminar de aire a presión, lo cual nos permite depositar altas cantidades de capa de estuco. Se emplea en papeles arte y altos brillos.
10. A continuación del estucado el papel se rebobina, eliminando posibles defectos y haciendo empalmes de posibles roturas.
Una vez bobinado el papel se le da el acabado que le corresponde a cada uno, pueden darse estos tres acabados distintos ó solo uno, (a parte del estucado) dependiendo del papel.
- Uno de los acabados es el calandrado; se trata de un conjunto de rodillos alternos metálicos (duros) y de fibras (blandos) que dan lisura por la presión y aportan brillo mediante la fricción. Este proceso se realiza en la calandra, fuera de la máquina de papel.
- Otra opción es el cepillado, que se hace en una máquina provista de grandes cepillos cilíndricos los cuales giran a gran velocidad aportando brillo aunque disminuyendo la porosidad del papel.
- En última instancia estaría el gofrado, en el cual se transfiere una textura en relieve al papel haciéndolo pasar entre rodillos metálicos portantes de la forma deseada.
Las bobinas madre se cortan y enrollan en otras más pequeñas. Si es necesario se utiliza la cortadora que transforma el papel de bobina en hojas. Tras ello se realiza el escogido manualmente para sacar los posibles defectos de fábrica no detectados.
Para enviarlo a los respectivos clientes se embala en bobinas y paquetes de remas que se tretactilan con plástico.
Para enviarlo a los respectivos clientes se embala en bobinas y paquetes de remas que se tretactilan con plástico.
CREACIÓN DE LAS CAMISAS:
No hay comentarios:
Publicar un comentario